3D Printing with Drones
Merging Additive Manufacturing with Aerial Agility – An Engineering Paradox 🦾
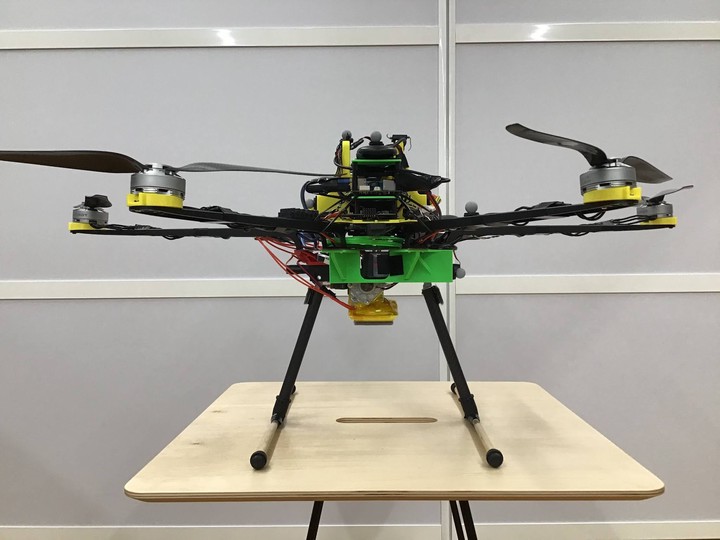
For most of my PhD research at the University of Texas at Austin, I explored the feasibility of integrating underactuated multicopters (a special type of drone) with 3D printing to enable large-scale and fully remote additive manufacturing. My research tackled fundamental questions regarding positioning accuracy, process synthesis, and practical implementation challenges, ultimately demonstrating the potential of aerial robotic systems as a novel alternative to ground-based 3D printing platforms.
Motivation
Unlike robots and other 3D printing machines, multicopters have the advantage of being unrestricted in 3D space and are more capable of reaching remote and inaccessible locations. Rapid advancements in controls and autonomy of multicopters are driving the use of multicopters for novel applications that go far beyond already established surveillance and mapping applications. Since multicopters do not suffer from the same limitations as ground-based robots, combining 3D printing with multicopters has the potential to address current limitations for printing large-scale 3D objects and repairing hard-to-reach infrastructure.

Figure 1 shows an example of how multicopters can benefit large-scale 3D printing. The pictured multicopters deposit cementitious materials to build architectural structures from the ground up. Each multicopter receives material from a storage vehicle and then flies to the desired print location, where the multicopter deposits the material. These multicopter-driven 3D printing systems can print large-scale objects more easily than ground-based 3D printing systems since the multicopters do not rely on the ground for support. Due to a multicopter’s compactness, the aerial 3D printing systems can also scale more easily in numbers.

Figure 2 illustrates how multicopters could provide fully remote repair capabilities for damaged infrastructure, such as tall buildings, bridges, and power equipment. Depending on the repair application, the multicopter could deposit new material to repair cracks or coat exposed surfaces to prevent further degradation. These systems could operate with minimal human intervention and be paired with inspection multicopters to allow maintenance operations for fully remote locations.
Key Research Questions and Contributions
The dissertation focused on two critical feasibility questions:
What positioning accuracy is required for large-scale and fully remote 3D printing, and what accuracy can multicopters provide?
What challenges arise from integrating multicopters with 3D printing processes?
To answer the first question, I developed a representative hexacopter testbed that will be tested on trajectories similar to what a 3D printing system would traverse. We then measured the positioning accuracy of the hexacopter testbed and compared the positioning accuracy with ground-based robotic systems previously deployed in large-scale and remote 3D printing applications. The results showed that the hexacopter’s accuracy exceeded that of nearly half of the ground-based systems and outperformed most robotic positioning setups with similar vertical reach (see Figure 3). Given the hexacopter’s ability to scale more easily in the vertical direction (see arrow in Figure 3), this result suggests that multicopters may be a promising candidate for large-scale and remote 3D printing.

To further refine the positioning accuracy analysis, I studied positioning accuracy under surface contact and tethered flight conditions, both potentially critical for ensuring precise and continuous material deposition in real-world scenarios. My findings indicated that surface contact can enhance vertical accuracy but degrade horizontal accuracy due to friction. Tethered flight, on the other hand, can improve the positioning accuracy of the hexacopter during flight, likely due to increased flight stability from the tether. However, the increased positioning accuracy comes with an overall decrease in positioning flexibility since the hexacopter is now connected to an external system.
The second feasibility question—focused on process integration—was addressed by designing and evaluating two 3D printing testbeds:
A fully onboard fused deposition modeling (FDM) system, where the multicopter carries both the printing apparatus and material (see Figure 4).
A tethered reactive extrusion additive manufacturing (REAM) system, where the material is supplied via flexible tubes to enable larger-scale printing.
Both testbeds successfully demonstrated the feasibility of aerial 3D printing. The FDM setup achieved accurate deposition of simple geometric contours but required precise control adjustments to counteract surface contact effects. The REAM system faced challenges related to material curing in the supply tubes, but it successfully deposited material in repeatable patterns, proving the viability of tethered deposition methods.
Broader Impact and Future Directions
The integration of 3D printing with multicopters has the potential to overcome significant robotic limitations in construction, maintenance, and disaster recovery. Future applications may include:
Printing large-scale structures using tethered multicopter setups.
Remote infrastructure maintenance in hazardous or inaccessible locations.
Deployable repair swarms for post-disaster reconstruction.
However, several challenges remain open for future investigation:
Outdoor Deployment: The experiments were conducted in controlled indoor environments with high-precision motion capture systems. Achieving similar accuracy in outdoor conditions is likely challenging without advanced sensing and disturbance rejection techniques.
Surface Contact Optimization: While surface contact improves accuracy in the normal direction, friction-induced disturbances must be mitigated through novel control strategies or rolling contact mechanisms.
Scalability and Vehicle Dynamics: Larger multicopters may exhibit different positioning characteristics, necessitating further studies on how scaling affects stability and accuracy.